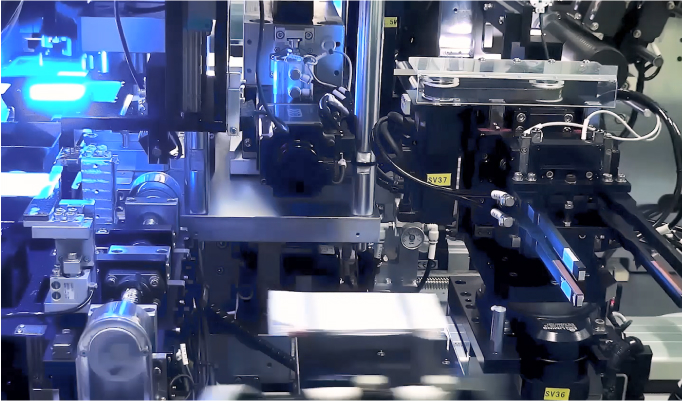
PTL Automation Equipment Division consolidates the advantages of high-speed double-sided coating technology, improves the self-sufficiency of key components, strengthens the lean management of manufacturing and delivery, and actively promotes the international market team and business layout. PTL Aactively entered the mid-segment winding, lamination, liquid injection and post-condensation market, transformed into a complete line solution provider, leveraged the capital market to integrate professional teams and new businesses, and established the battery complete line solution platform layout.
This equipment is suitable for the coating process of positive and negative electrodes in the production of lithium-ion batteries with 1400mm width, 4.5μm, 100m/min. It can realize closed-loop thickness adjustment, automatic glue sticking, Aautomatic loading and unloading of coil material, real-time comprehensive monitoring of coating size, surface density, equipment status, etc., to improve qualification rate and utilization rate.
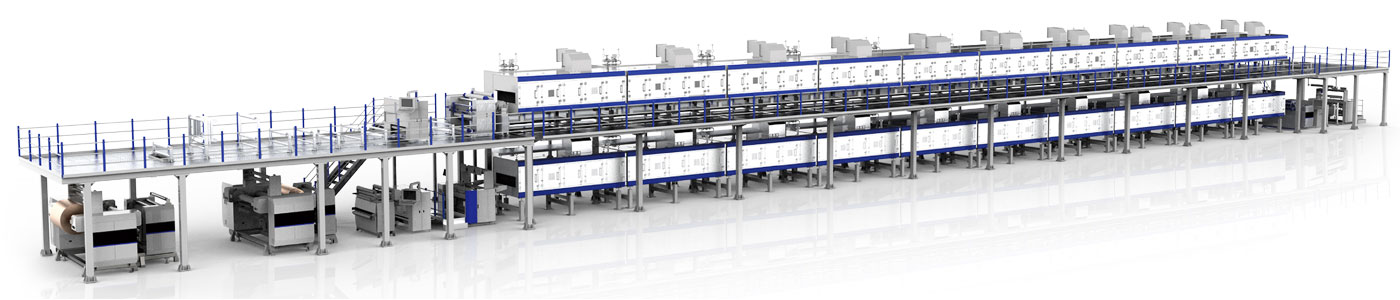
-
Double Layer Gravure Primer
It is suitable for the coating of the underlying modified material of the lithium-ion battery substrate, which realizes continuous, intermittent and zebra coating, and can be used together with the pole piece coating machine.
-
Separator Coater
This equipment is suitable for lithium-ion battery Separator ceramic layer and PVDF coating in battery production. The stirred slurry is evenly coated on the Separator, and it winds up after drying and finishing organizing to ensure that the product size, thickness and appearance meet the design specifications.
-
Single Layer Extrusion Coater
The equipment model is optional for single/double-sided models, the overall size of the equipment is 47000*3000*3100mm, the width of the substrate is 700mm, the length of the oven is optional, and electricity/conducting oil/steam is used as the heating method.
-
Slitting Machine
The equipment is used for the slitting process of lithium-ion battery separator pole pieces. There is a spiral reciprocating edge material recovery mechanism, which greatly reduces the operation time of edge material unloading and improves the OEE of the equipment. The upper straight knife, the lower straight knife and the circular knife can be switched to each other to adapt to different Separators.
-
Winding Machine
With independent polygon winding needle patent, circular winding can be realized;
It has a multi-level high-precision deviation correction system, and accurately detects the alignment of the opposite sides through CCD imaging, which can better control the alignment between the pole piece and the Separator, reduce overhang defects, and improve the yield of finished equipment.
-
Filling Machine
The industry's first high-efficiency vibration differential pressure injection, the efficiency is improved by >40%, the static process time is shortened by 30%~50%, and the secondary injection volume is reduced;
The equipment is mainly used for injecting quantitative electrolyte into square aluminum shell batteries, which can automatically scan the battery barcode, weigh before injection, inspect Hi-pot, achieve vacuum injection, weigh and read code after injection, wipe, seal injection port, unload etc.
-
Double Head High Speed Stacking Machine
Powerful software functions: stepless speed regulation, dynamic display of each mechanism, one-click model change;
First in Industry: the first Separator positioning, completely solved the major defect in stacking production;
Speed: Single-station stacking takes 0.5 seconds/piece stably, which is 100% faster than other domestic equipment;
-
Formation and Grading Equipment
This equipment is used for cell heating: pressure formation, capacity, including cell air bag leveling, flipping, cell code scanning, formation, capacity, discharging and sorting, etc. It is suitable for soft-pack batteries production. It loads and unloads with magazines, compatible with scanning code on both sides.